Book Downloads Hub Reads Ebooks Online eBook Librarys Digital Books Store Download Book Pdfs Bookworm Downloads Book Library Help Epub Book Collection Pdf Book Vault Read and Download Books Open Source Book Library Best Book Downloads Yigal Kipnis Paul Kemp Robertson Gilles Dowek Bhat Boy Wj Orion Jaume Guilera Megan Shepherd Thich Nhat Hanh
Do you want to contribute by writing guest posts on this blog?
Please contact us and send us a resume of previous articles that you have written.
7 Foolproof Strategies to Eliminate Human Errors in Production and Service Processes for Unmatched Efficiency and Quality

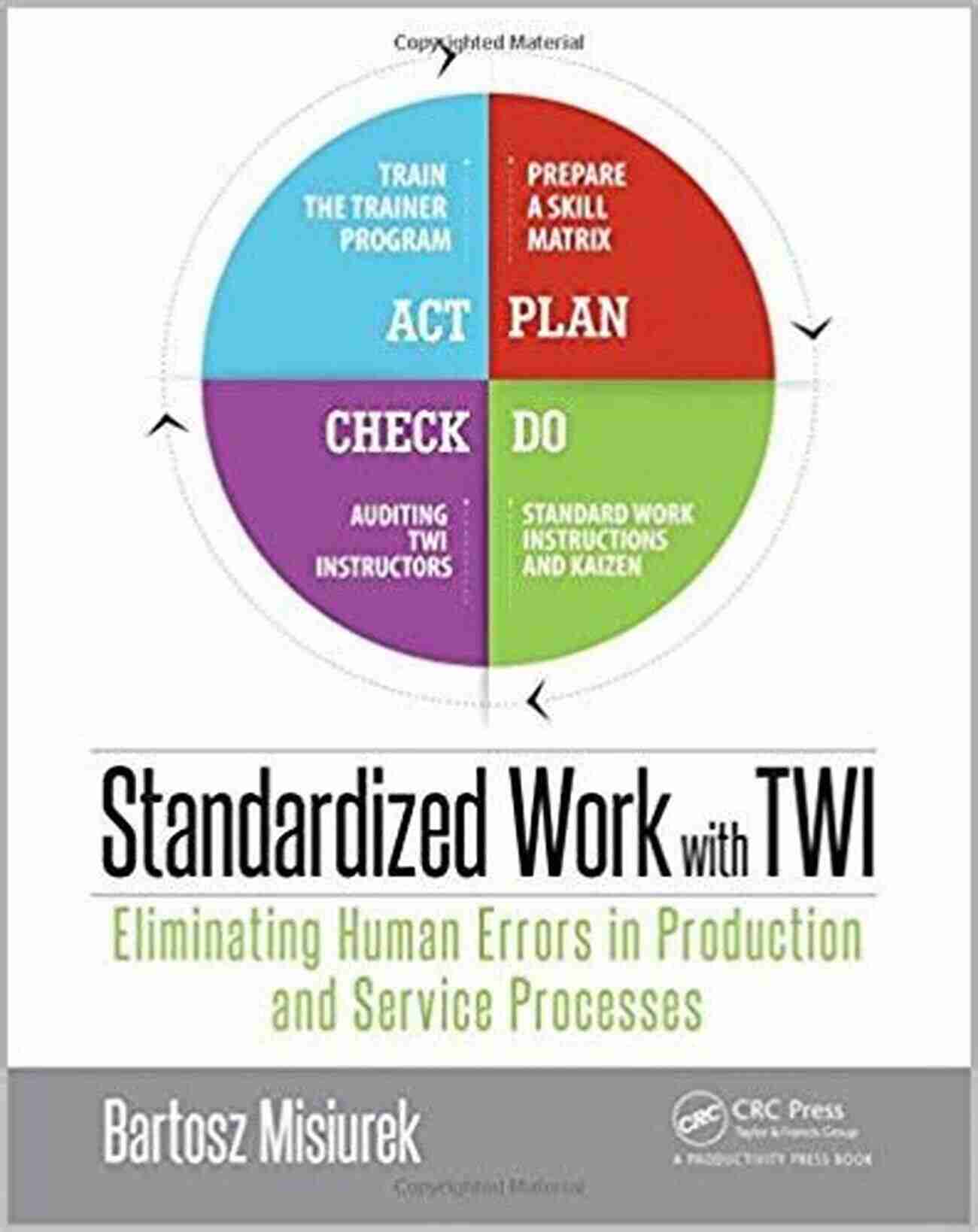
Human errors have long been a significant concern in both production and service processes, leading to inefficiency, quality issues, and potential customer dissatisfaction. However, with the advancements in technology and the implementation of robust strategies, businesses can now significantly reduce human errors and elevate their operations to new heights.
1. Automation: Enhancing Precision and Accuracy
One of the most effective ways to eliminate human errors is through automation. By replacing manual tasks with automated processes, businesses can minimize the risk of mistakes caused by human intervention. Automation enhances precision and accuracy, ensuring consistent quality throughout the production and service processes.
2. Training and Skill Development: Equipping Employees with Knowledge
Investing in training and skill development programs for your workforce is crucial in reducing human errors. Providing employees with the necessary knowledge and skills not only improves their individual performance but also equips them to handle complex tasks with greater efficiency. Regular training sessions and workshops can address specific areas prone to errors, helping employees stay updated with industry best practices.
4.2 out of 5
Language | : | English |
File size | : | 14986 KB |
Print length | : | 191 pages |
Screen Reader | : | Supported |
3. Implementing Standard Operating Procedures (SOPs)
Standard Operating Procedures (SOPs) play a vital role in eliminating human errors across various processes. By documenting and following standardized protocols, businesses can ensure consistency and reduce the probability of errors. Clear instructions and guidelines enable employees to perform tasks accurately, minimizing deviations that could lead to mistakes.
4. Quality Control Measures: Real-Time Error Detection
Integrating robust quality control measures in production and service processes is imperative to catch errors in real-time. Implementing checkpoints, inspections, and quality assurance procedures allows businesses to identify and rectify human errors promptly. By constantly monitoring output quality, businesses can prevent errors from escalating into major issues, ensuring customer satisfaction.
5. Continuous Improvement Culture: Encouraging Innovation
Embedding a culture of continuous improvement within the organization fosters innovation and allows for the identification and elimination of human errors. Encouraging employees to share ideas for process optimization and error prevention empowers them to actively contribute towards enhancing efficiency and quality. Creating an open and supportive environment enables teams to take ownership of their actions and strive for ongoing improvement.
6. Task Prioritization and Time Management
Overloaded schedules and improper task prioritization can contribute to human errors. By implementing effective time management strategies and organizing workflows, businesses can reduce the likelihood of mistakes caused by rushed or neglected tasks. Providing clear priorities and realistic deadlines helps employees manage their workload efficiently, resulting in improved accuracy and reduced errors.
7. Communication and Collaboration: Strengthening Teamwork
Effective communication and collaboration among team members play a crucial role in eliminating human errors. Encouraging open dialogues, fostering a supportive work environment, and promoting teamwork allow for the identification and resolution of potential errors at an early stage. Regular team meetings, where concerns and challenges are addressed, help in streamlining processes and reducing errors caused by miscommunication or lack of coordination.
Eliminating human errors in production and service processes is an ongoing endeavor that requires a proactive approach and a combination of strategies. By embracing automation, investing in employee training, implementing SOPs, focusing on quality control, fostering a culture of continuous improvement, prioritizing tasks, and enhancing communication and collaboration, businesses can significantly reduce human errors and achieve unparalleled efficiency and quality. The journey towards error-free operations ultimately leads to increased customer satisfaction and a competitive edge in the market.
4.2 out of 5
Language | : | English |
File size | : | 14986 KB |
Print length | : | 191 pages |
Screen Reader | : | Supported |
Standardized Work with TWI: Eliminating Human Errors in Production and Service Processes presents the Training within Industry (TWI) program and describes how it can influence and alter one’s understanding of work standardization. Work standardization is the key to eliminating human errors from manufacturing and service processes. Work standardization is not just the creation of job instructions—it is a comprehensive approach in which employees are formally trained and their skills in the area of work improvement are developed by kaizen sessions. With poor instructions, though, the effectiveness of these two key activities in the work standardization process is practically impossible to achieve.
The book introduces you to 41 rules for standard work instruction (SWI) preparation. Following these rules will ensure that the instructions in your company are ideally suited to train operators and improve work. The author developed these rules based on his professional experience and practice within the TWI program in more than 120 manufacturing and service enterprises, while creating thousands of SWIs. These rules are a clear set of signposts that will help you develop a correct SWI on the first attempt without any unnecessary correction of errors. The quality of SWIs significantly affects how on-the-job training sessions are run, as well as how work analysis with respect to improvement is conducted.
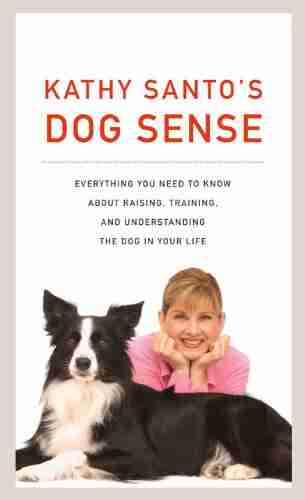

Kathy Santo Dog Sense Kathy Santo - Unlocking the secrets...
Are you a dog lover who...
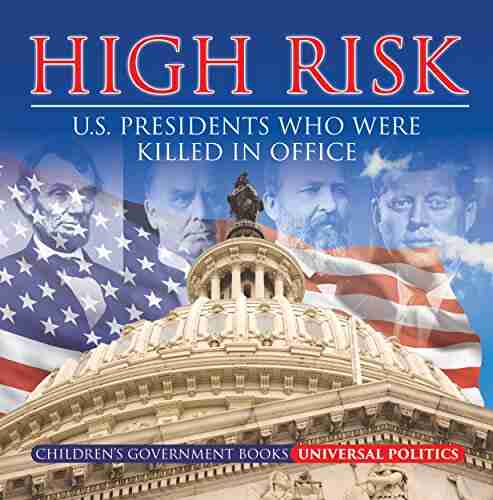

10 Presidents Who Were Killed In Office - Shocking Truth...
Throughout history, the role of a president...
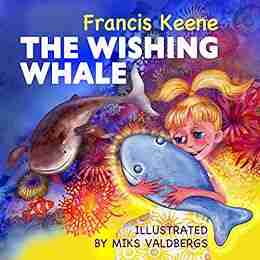

Unveiling a World of Magic: Beautifully Illustrated...
Bedtime stories have always held a...
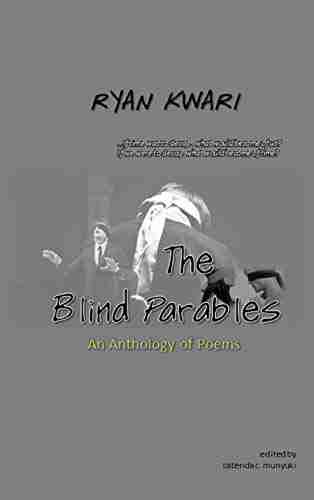

The Blind Parables: An Anthology Of Poems
For centuries, poetry has...
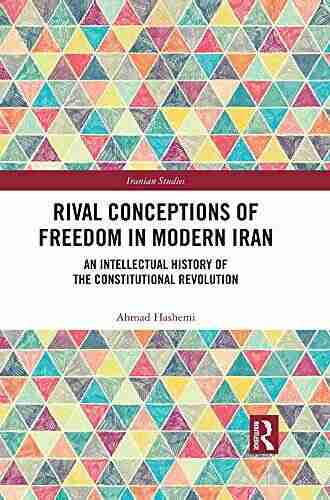

Rival Conceptions Of Freedom In Modern Iran
The Struggle for Freedom in...
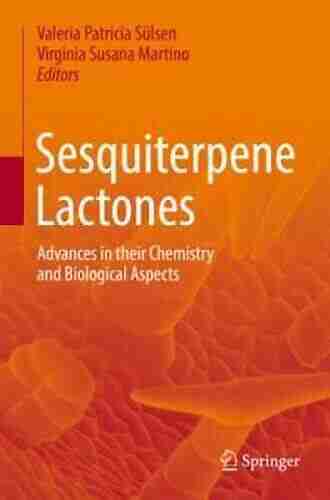

Advances In Their Chemistry And Biological Aspects
In recent years,...
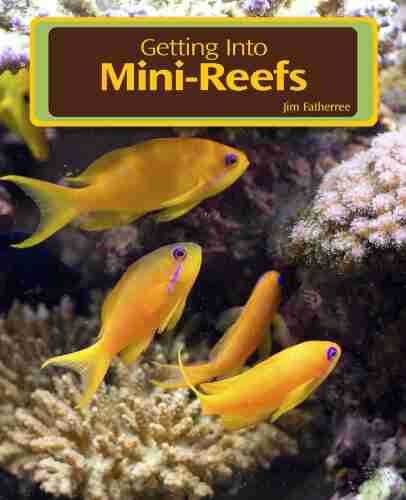

Getting Into Mini Reefs For The Marine Aquarium
Are you interested in enhancing the...
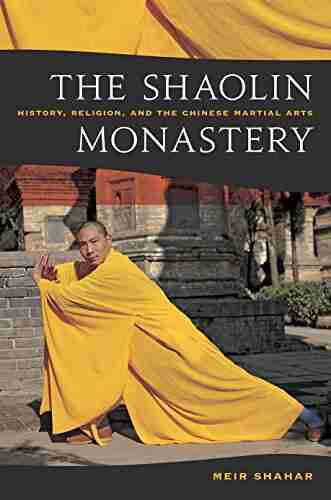

Exploring the Intriguing Connection Between History,...
When one thinks of Chinese martial...
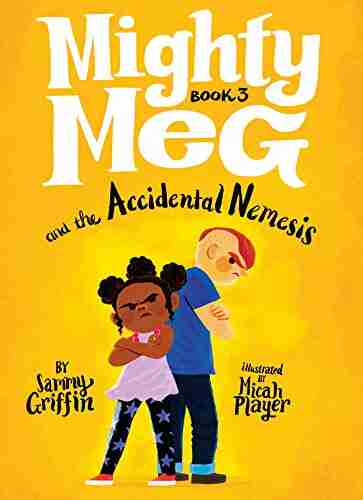

Mighty Meg And The Accidental Nemesis: Unleashing the...
In the world of superheroes, there are many...
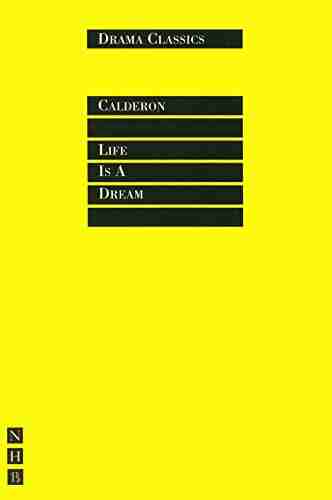

A Journey through the World of Nhb Drama Classics: Full...
Welcome to a fascinating exploration of Nhb...
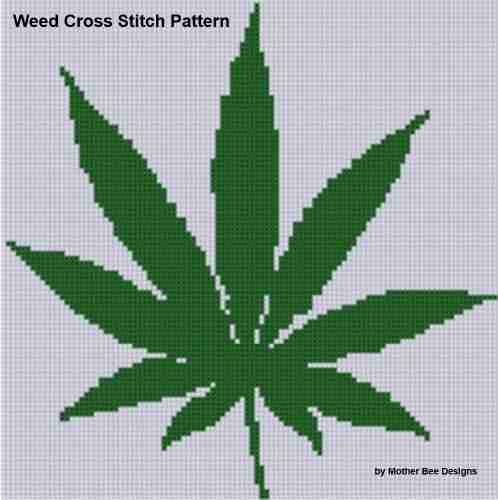

Weed Cross Stitch Pattern Rachel Worth - The Perfect...
Are you a stoner who loves a little...
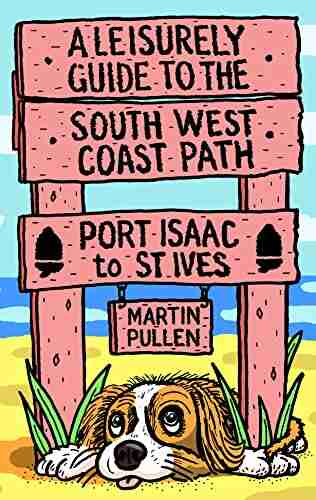

Discover the Breathtaking Beauty of the South West Coast...
Are you ready for an...
Light bulbAdvertise smarter! Our strategic ad space ensures maximum exposure. Reserve your spot today!
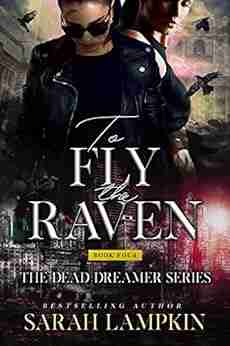

- Gus HayesFollow ·17k
- David BaldacciFollow ·9.4k
- Dwight BlairFollow ·8.5k
- Salman RushdieFollow ·4.2k
- Henry GreenFollow ·17.1k
- Steve CarterFollow ·16.7k
- Eddie PowellFollow ·17.2k
- Clark CampbellFollow ·14.2k